Toyota team members have always been directed by the company's guiding principles of continuous improvement, known to us as KAIZEN, and elimination of MUDA, or elimination of any waste from the process of manufacturing our vehicles. But did you know that our relentless focus on KAIZEN and eliminating MUDA extends well beyond our manufacturing operations? We recognize that our building footprint is significant, and our work to minimize and optimize its environmental impact is, therefore, directed by these same Toyota guiding principles.
As our physical building footprint started increasing in the late 1990‘s, we made a concerted effort to apply environmental guidelines and our guiding principles to the way we design, construct and operate our facilities. The goal was to ensure the application of sustainable practices in our projects. This approach was used in 2000 as design began for the former Torrance, California, headquarters campus expansion known as South Campus. This 643,000 square-foot project increased the size of the headquarters campus by 47 percent and, when completed in 2003, was the largest commercial LEED Gold® building in the world. South Campus was also home to what at the time was the largest commercial rooftop solar photovoltaic system as well as many other sustainable features.
Since then, our North American real estate holdings have grown, and several facilities have undergone expansions. During this time, we have continually refined our approach to green building and construction.
So, in 2014, when it was announced that Toyota would be reorganizing and relocating, we were ready to scale up our approach to green building.
REFINING OUR GREEN BUILDING APPROACH
We aimed to incorporate the highest levels of sustainable features in all aspects of three campuses: the new North American headquarters campus in Plano, Texas; the new Production and Engineering Manufacturing Center in Georgetown, Kentucky; and the new Supplier Center in York Township, Michigan. These are the key steps we took as we progressed through designing, constructing and commissioning our new campus:
- Set project-specific sustainability vision and aspirational goals.
- Addressed Toyota Motor North America’s four environmental focus areas of Carbon, Water, Materials and Biodiversity.
- Took an integrated and holistic design and delivery approach to ensure participation from designers, engineers, contractors and user stakeholders at project conception and continually through completion and commissioning.
- Challenged the project team to be innovative and aspire for leadership in environmental sustainability.
- Reviewed various third-party certification programs for their best practices and guidance.
- Used a deductive approach rather than an additive approach to sustainability.
- Evaluated possibilities and implemented options based on long-term environmental performance and financial value as well as initial cost.
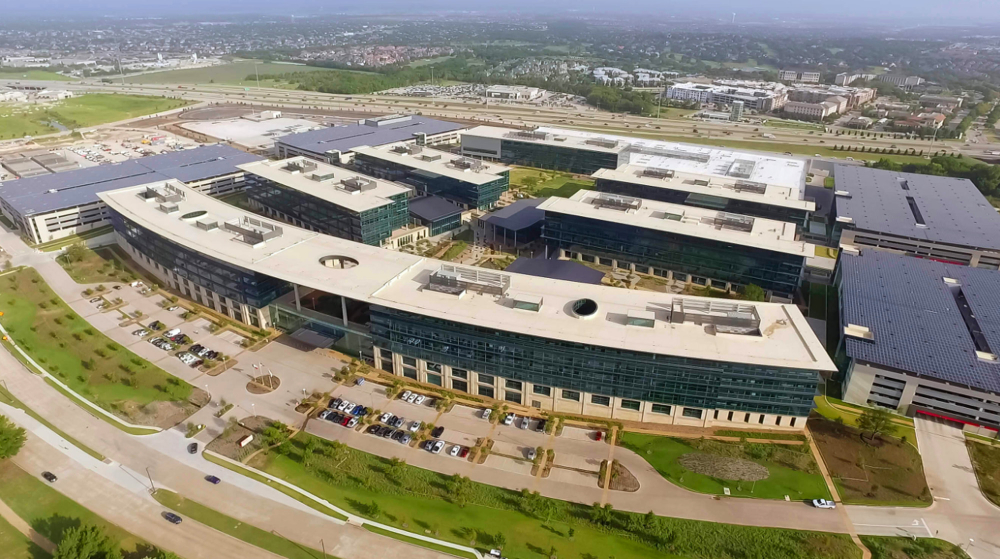
Toyota‘s North American headquarters campus was recognized by the U.S. Green Building Council with the award of three LEED Platinum® certifications.
For all three campuses, the vision and goals were set at the very beginning. These included visions of being net positive for renewable energy and net positive for water. Net positive means we would generate more electricity than we use and collect more rainwater than the total amount of water we use. In fact, as part of the Request for Proposal process, candidate architectural firms had to describe how their company and their design would address and respond to these visions of net positive. They had to show how closely they could design a campus that moved beyond just minimizing environmental impacts to one that actually would have a positive impact on the local community.
Integrated sustainability was incorporated into the very early stages of conceptual design using a deductive approach. This meant that we aimed to leave “no stone unturned” in looking at incorporating sustainable design and systems opportunities. All options were discussed and evaluated from the beginning.
While every option was discussed, not everything made sense for the project. For instance, using a geothermal system to assist the Plano buildings’ cooling system seemed like a good idea to reduce electricity consumption. A good idea, that is, until analysis showed, due to the heavy cooling load imposed by the hot northern Texas summer, the ground temperature would be raised by two degrees!
Wind power in Texas seemed to make sense until we realized the wind turbine blades would be more than 300 feet in diameter and their noise level would not be so neighborly.
EARNING LEED PLATINUM®
Our efforts have been recognized by the U.S. Green Building Council with the award of three LEED Platinum® certifications for the Plano campus, plus LEED Platinum certifications for PEMC and the Supplier Center in York Township.
Examples of features that earned LEED Platinum certifications include:
- CARBON — All three locations installed solar photovoltaic panels to generate renewable energy that supports their electrical needs and reduces their carbon footprint. At PEMC, we installed a 436 kilowatt solar photovoltaic system. Additionally, the mega-trellis design of the façade minimizes heat gain in the summer and maximizes it in the winter for energy efficiency.
- WATER — At the Plano headquarters campus, we installed a rainwater harvesting system that at the time of installation was the largest commercial system in the U.S. The collected rainwater provides water for landscaping irrigation.
- MATERIALS — During construction of the Plano campus, we recycled 99 percent of the construction and demolition waste and were the first customer at the first construction and demolition recycling processing facility in northern Texas.
- BIODIVERSITY — The Supplier Center‘s biodiversity program earned a Conservation Certification from the Wildlife Habitat Council in 2017. The site has a large stormwater retention pond supporting migratory birds and other species, and a grasslands and wildflower habitat area covers 76 acres.
And, many of our dealers have followed our lead. In fact, we have more Toyota/Lexus LEED-certified dealerships than our competitors combined.
LOOKING AHEAD
We’ve learned a great deal from these experiences, and we are applying our learning to other projects. We continue to refine our approach to green building, looking for ways to minimize the environmental footprint of our buildings and maximize our positive impacts. Not all projects will pursue LEED certification, but all will aim to incorporate sustainable features to the greatest practical extent.
These actions support the Toyota Environmental Challenge 2050, which aims to go beyond merely minimizing environmental impact to creating net positive change. We look forward to sharing additional green building successes in the future, including the renovation of our vehicle logistics facility at the Port of Long Beach in California, the construction of a new visitor center at the assembly plant in Mississippi, and the construction of a new parts distribution center in Clarington, Ontario. All three projects are submitting for LEED® certification.
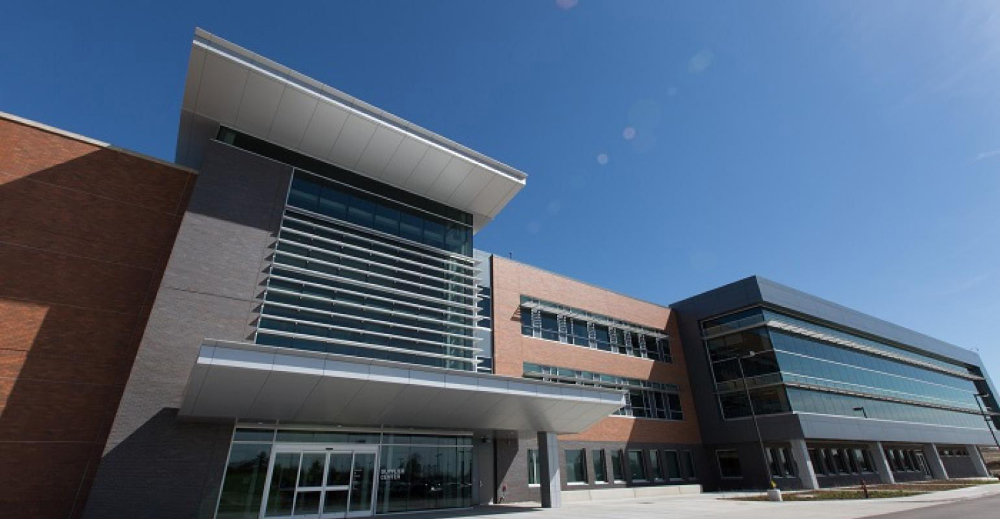
The Toyota Supplier Center in York Township, Michigan, was awarded Platinum LEED® in April 2019.
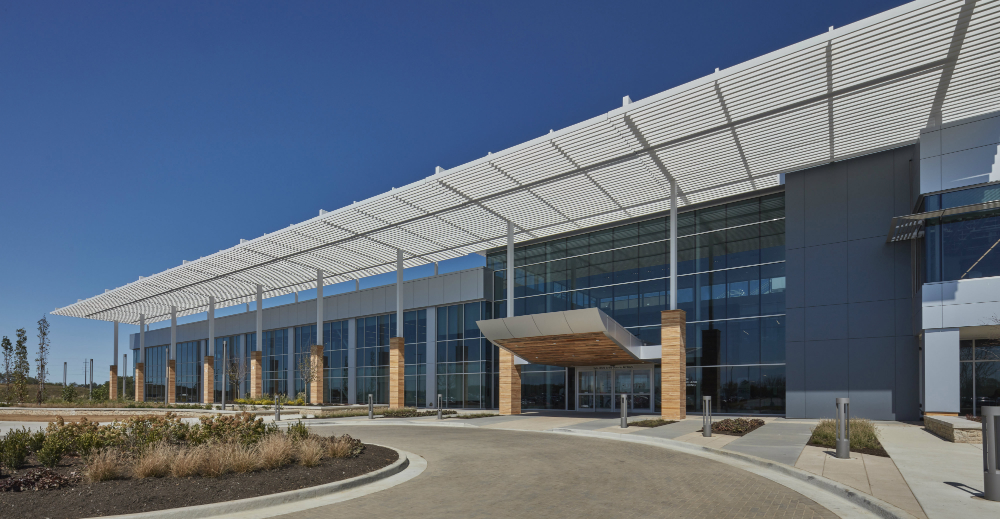
The Toyota Production Engineering and Manufacturing Center in Georgetown, Kentucky, was awarded Platinum LEED® in April 2019.

Mark Yamauchi
LEED AP®
Manager, Environmental Sustainability
Toyota Motor North America, Inc.